Next-Generation Vehicles Pose Automotive Semiconductor Test Challenges
By Jerry Koo, Advantest Korea Co., Ltd., Business Promotion Division, Team Leader
Introduction
Various market trends are driving requirements for automotive semiconductor test as technology increasingly defines the future of the automobile. According to IHS Markit,1 the total market for semiconductors, having reached nearly $500 billion in 2018, will grow at a CAGR of 4.88% through 2022, while the automotive electronics category, reaching more than $40 billion in 2018, will outpace the total market, growing at a CAGR of 8.74% through 2022.
This market growth accompanies a paradigm shift toward the technologies that define the future of next-generation vehicles.
Alternative propulsion systems include hybrid and EV drivetrains and will require a new charging/refueling infrastructure, possibly including wireless charging, and will be accompanied by efficient motor drives, car weight reduction, and a move to 48-V batteries. To ensure high quality, it will be necessary to thoroughly test sensors, MCUs, power devices, power-management ICs, and other related components.
Connected cars will feature IoT, GPS, and cellular connectivity to enable infotainment and telematics functionality while integrating media, smartphones, and apps. Communications will extend beyond the car to other vehicles and infrastructure and to datacenters in the cloud.
Vehicles will also require various highly accurate sensors to enable ADAS and fully autonomous vehicle functionality. Complementing cloud connectivity will be high-speed networks within the car and onboard high-performance computing. Technologies will evolve from driver assistance in 2015 to automation (with the car operating as a copilot) driven by sensor fusion in 2020 and on to fully autonomous operation in 2030.
All these technologies will impose on auto manufacturers cost-management and product-planning challenges on the factory floor, in the car, and throughout the supply chain, leading to zero defects from the process to the field.
High voltage and parallelism
High-voltage semiconductor processes for automotive propulsion and cost management include 0.32-μm to 1.0-μm high-voltage (700 V) bipolar-CMOS-DMOS (BCD), 0.18-μm to 0.32-μm (200 V/300 V) SOI BCD, and 0.18-μm to 0.35-μm (80 V/150 V) BCD. Semiconductors fabricated in these processes serve applications areas extending from EV and HEV powertrain to braking, airbag-deployment, and other safety/body functions.
To test such semiconductors, Advantest offers T2000 IPS test modules, including the MMXHE (120 V), the MFHPE (300 V), and the SHV2KV (2,000 V) as well as the EVA100 Evolutionary Value-Added Measurement System, which offers analog VI sources providing outputs to 96 V as well as medium- and high-power VI sources offering outputs to 128 V and 2,000 V, respectively (Figure 1).
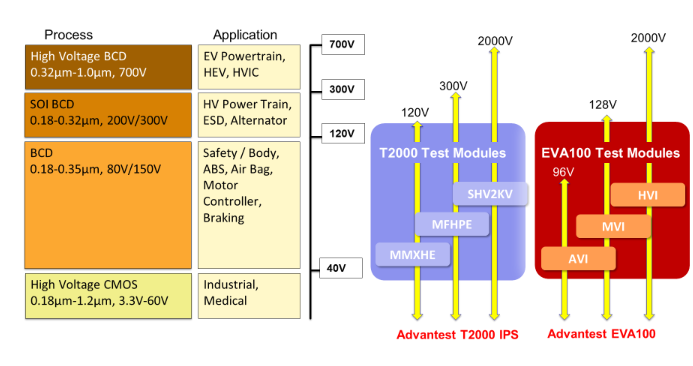
Figure 1. T2000 and EVA100 modules facilitate the test of semiconductor devices for a variety of automotive applications, from the powertrain to safety and body systems.
Compared with alternatives, the T2000 MMXHE enhanced multifunction mixed high-voltage module offers a simple board design with high parallelism, including 64 cross-functional ports, offering PMUs, 10-ps-resolution TMUs, 32 digitizer channels, and 32 AWG channels. It supports IDDQ test as well as 20-bit differential voltage measurements.
The T2000 MFHPE multifunctional floating high-power module can operate in single, gang, and stack configurations with up to 18 channels or 36 ports per module to support multisite test.
T2000 IPS supports highly accurate and highly parallel automotive PMIC test, with only two modules able to perform DC/DC converter tests, LDO tests, and MCU I/F functional tests. A key benefit of the T2000 IPS is its minimization of test-board components (such as buffers and electromechanical relays), thereby simplifying PCB design and maintenance (Figure 2).
Figure 2. The T2000 IPS minimizes the number of components required on a test board, thereby easing board design and system maintenance.
Sensor test
Autonomous vehicles present the need to test highly accurate sensors, including CO2 sensors, airbag pressure sensors, vehicle-stability-control (inertial) sensors, and pedestrian pressure sensors. Automotive angle sensors (for electric power steering and integrated starter-generator applications) present particular test challenges, requiring extensive screening to ensure accuracy and reliability. For such applications, the Advantest EVA100 provides the necessary fF and pA testing capabilities.
Electric, hybrid, and plug-in hybrid-electric vehicles also incorporate current sensors to monitor main and auxiliary batteries as well as inverters, motors, and chargers. Conventional methods of testing these sensors, including the use of current clamps or Helmholtz coils, have drawbacks. The Helmholtz-coil method, for example, presents challenges related to magnetic flux intensity and uniformity, and it requires a large chamber (1.5 x 1.5 x 1.5 m) to keep the coils and DUTs at the required -40°C temperature. In contrast, a new high-current sensor-test method based on the Advantest EVA100 offers a 20-fold size reduction (600 x 500 x 300 mm) while testing four DUTs in parallel. The method employs dual-fluid direct temperature control; electromagnets apply guaranteed magnetic flux levels to the DUTs.
SiPs and system-level test
Connected cars are driving a trend toward the increasing integration in automotive modules, SiPs, and SoCs. Such devices increasingly integrate processors and memory as well as imaging, magnetic, or pressure sensors; power devices and MCUs; memory and MCUs; MCUs plus baseband and RF circuits as well as antennas; and motor drivers and MCUs. SiPs present many technical test challenges related to interposer connectivity, warpage, die shifting, die-to-die communications (with marginal timing), limited test ports on the package, package handling, and stress related to level, timing, and processing.
Such highly integrated devices impose stringent test requirements. System-level test (SLT) can play a role in boosting quality, coming after wafer sort and final test and before installation in the end product. However, legacy SLT environments based on rack-and-stack equipment can be cumbersome and slow. In contrast, the Advantest T2000 SLT Solution automates SLT, enabling a compact SLT cell for high-mix low-volume devices or a large-scale SLT cell for ultrahigh-volume production and long SLT times.
Conclusion
From sensors and processors to power-management and motor-controller ICs, semiconductors for next-generation automotive applications will present significant test challenges, including SLT. Advantest’s T2000 IPS and EVA100 systems are available today to meet the test requirements of the devices that will serve in tomorrow’s hybrid, electric, and autonomous vehicles and the infrastructure that supports them.
Reference
1. “Semiconductor Application Forecast AMFT Intelligence Service,” IHS Markit Technology Group, Q4 2018.